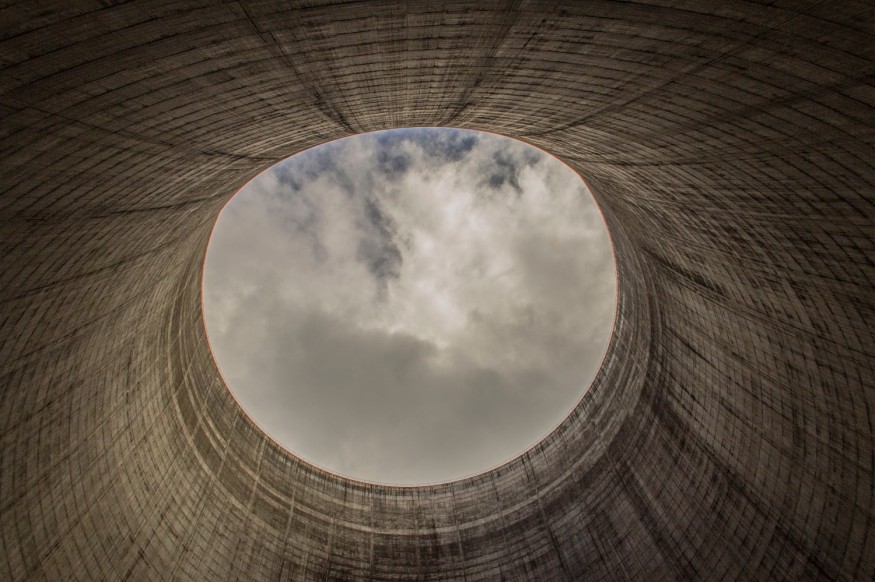
Scientists from National University of Science and Technology (NUST) MISIS have developed durable, unique composite material that can withstand harsh temperature conditions like in nuclear reactors. The unique composite material can be three times higher than the microhardness of the components that were used to put it together. The results of the study have been published in Materials Letters. In this article, explore what the scientists have created and how the new discovery will help innovation.
New materials are needed to produce a new generation of fast-neutron reactors. Though steel has always been a popular option in creating shells of fuel elements, it is no longer viable as it could not withstand the amount of heat required, extreme heating that could be within the range of 550 to 700 degrees Celsius.
Initially, to create a harder composite material, it requires to use the method called the Severe Plastic Deformation (SPD). In this method, the material will be put in a machine where it can be exposed to extremely high pressure. Thus, it makes the material harder. By using the same process, the scientists have created an improved nanocrystalline structure of the material, which basically demonstrates the possible rapid growth in the material when heated. However, this process creates a material that has low thermal stability, which in turn makes it lose microhardness altogether too. This was a problem they had to resolve, so the team looked into the nanostructure of the materials they were working on.
A group of scientists for Hybrid Nanostructured Materials from NUST MISIS Laboratory discovered a new way to increase the thermal stability without compromising the microhardness of a composite material. They particularly used the high-pressure torsion (HPT) method, which allowed them to create a specific multilayer structure using a vanadium alloy.
"We had created a sample material that measures 0.3mm and 0.5mm layer of solid steel. The team then added in between a 0.2mm vanadium alloy. The overall thickness of the sample is about 1mm. Pressure has been applied to this thick combination and it resulted to a thin but rather multilayer structure of a material," said Stanislaw Rogachev, research head.
The materials were put together like a sandwich one layer on top of another. The "sandwich" created by the testing resulted to a material that the researchers have expected. Its strength has increased three times more than the strength of the individual components that were put together to build the material. For the first time, a composite material sandwiched in the nanostructure level with high thermal stability has been obtained. The final material testing involves its exposure to extreme heat of about 700 degree Celsius. It survived the heat and for the first time, the composite nanostructured material came with high thermal stability.
The promise of the material to be useful in a number of high-tech areas is within arm's reach. The scientists plan to move their research further by looking into steel–copper and steel–aluminum combinations.