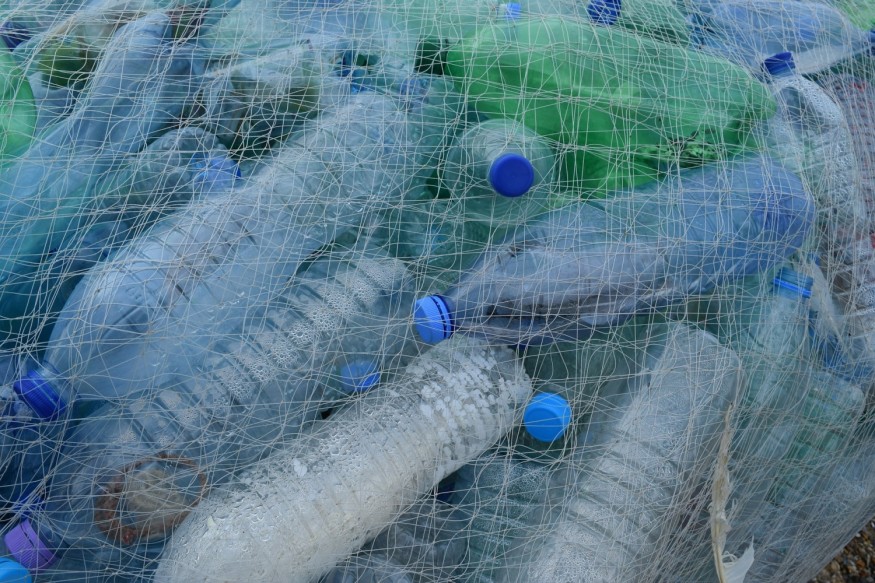
Plastic is not a bad material. In fact, the invention of plastic has had enormous impacts on several industries, making products and services more accessible than ever before. The problem lies in how we dispose of it. Only 14% of end-use plastics are recovered, leaving the rest to accumulate in landfills, enter waterways, or become incinerated.
Instead of the linear economy model, where plastics are thrown away after fulfilling their purpose, the world is making a shift towards a circular economy model, where plastic waste is eliminated and recycled for continual use.
But plastics have limitations in this circular economy model. Over time, repeated use and recycling of these plastics break down its polymer chain components. As a result, recycled plastics tend to degrade in quality over time, eventually becoming unusable.
By overcoming this degradation limitation, plastics can then become a truly circular material.
Researchers from Chalmers University of Technology in Sweden may have found a way to surmount this limitation. Published in Sustainable Materials and Technologies, the research group were able to recover 100% of carbon from plastic waste and turn it back into its virgin components.
The answer lies in steam cracking, an often-used method in the petrochemical industry, where steam and heat are introduced to break down organic molecules into their hydrocarbon components, which is what most plastics are made of. Now in the form of a gas mixture, the carbon can then be recovered to create the components of virgin plastic again. By using this existing method in generic petrochemical infrastructure, the study looks at how plastic factories can also be repurposed to recycle plastics as well.
By optimizing the parameters of the process, to a temperature of 850°C and a sufficient rate of heating and time in the reactor, the research group was able to recycle over 200 kilograms of plastic waste and recover their carbon components in as little as an hour. The plastics are then back to their original quality as when they first left the processing facility.
They found that switching to plastic waste as feedstock, instead of virgin plastic, for creating new plastics provides economic advantages and is technically feasible. However, implementation of the system relies on several factors, such as the regulatory framework in place to support these systems.
Henrik Thunman, who leads the research group, shared his insights into the importance of this technology in a press release from Chalmers University of Technology:
"Circular use would help give used plastics a true value, and thus an economic impetus for collecting it anywhere on earth. In turn, this would help minimize the release of plastic into nature, and create a market for collection of plastic that has already polluted the natural environment."
The Chalmers researchers are now looking to scale the process even further. With the success of their further research, there's a good possibility that this could see commercial use in the future.
With more developments being made to transition to a circular economy, the world remains hopeful that more advancements in sustainability could be a way to not only tackle the plastic problem on a large scale but also reducing the dependence on fossil fuels.
© 2025 ScienceTimes.com All rights reserved. Do not reproduce without permission. The window to the world of Science Times.