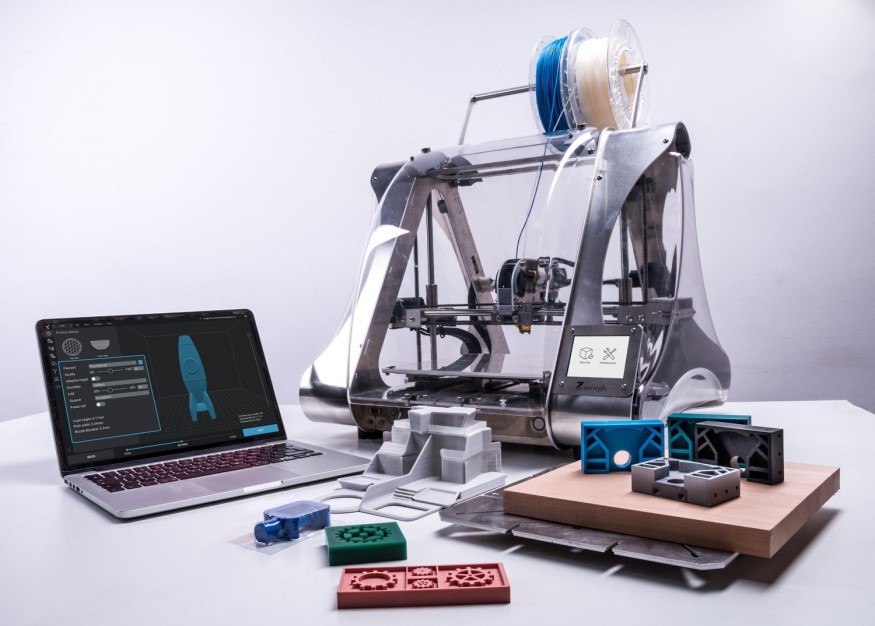
Prototyping and building parts for the aerospace industry is a process that has typically taken weeks, if not months to achieve. One British firm has now slashed this time to mere days thanks to a new 3D printing process using chrome cobalt.
The process of creating components from alloy metal is challenging due to the nature of the material. When a material is hard-wearing and capable of withstanding temperatures up to 600°C it can be difficult to use methods like CNC machining to create parts. By starting with a chrome cobalt powder, it's possible to achieve incredibly intricate designs with any shape or geometry required.
To achieve this Protolabs employs a process known as direct metal laser sintering. This can produce precise resolution parts, down to a minimum feature size of 1.00mm and a minimum wall thickness of 1.00mm.
The direct metal laser sintering process
Direct metal laser sintering is a process which can turn powdered metal into super-strong and precise designs. This 3D printing process takes place in a sealed chamber filled with an inert gas to help eliminate the risk of combustion. A computer-controlled high-powered laser beam fuses layers of the chrome cobalt powder. The design is built up in layers, similar to selective laser sintering, but this process uses metal powder instead of a polymer.
This process is faster than CNC machining and can also produce more precise results. It's also possible to achieve far more intricate designs, such as a honeycomb structure. This is perfect for reducing the weight of components or increasing the strength. The material can be polished to a smooth surface, making it ideal for the aerospace industry. And because the process can be completed quickly, prototyping new components becomes a lot more rapid.
Advantages of 3D printing chrome cobalt
Cobalt chrome is an alloy of chromium and cobalt. It is known for its high strength to weight ratio. In an industry that relies on components that are lightweight and strong, this can be a game-changer. This material can withstand temperatures up to 600°C while also offering high creep and corrosion resistance.
According to Protolabs, parts created using DMLS are equal to or better than those of wrought materials. It's also worth noting that DMLS can also achieve geometry and structure that simply isn't possible with other manufacturing processes.
This could be a key development not only for the aerospace industry but for other sectors which require precise and intricate designs. One example of this is the medical industry. Chrome cobalt is already used for creating orthodontic implants and orthopaedic components. The Protolabs approach could make this process faster and more customisable, allowing for more intricate designs which are more suited to osseointegration. The designs could also be created unique to each patient, allowing for a better fit and simpler surgical procedure.
Chrome cobalt isn't the only material which can be 3D printed by Protolabs. They are also using copper, Inconel, maraging steel, stainless steel and titanium. This is alongside a range of CNC machining materials including aluminium, brass and carbon steel.
© 2025 ScienceTimes.com All rights reserved. Do not reproduce without permission. The window to the world of Science Times.