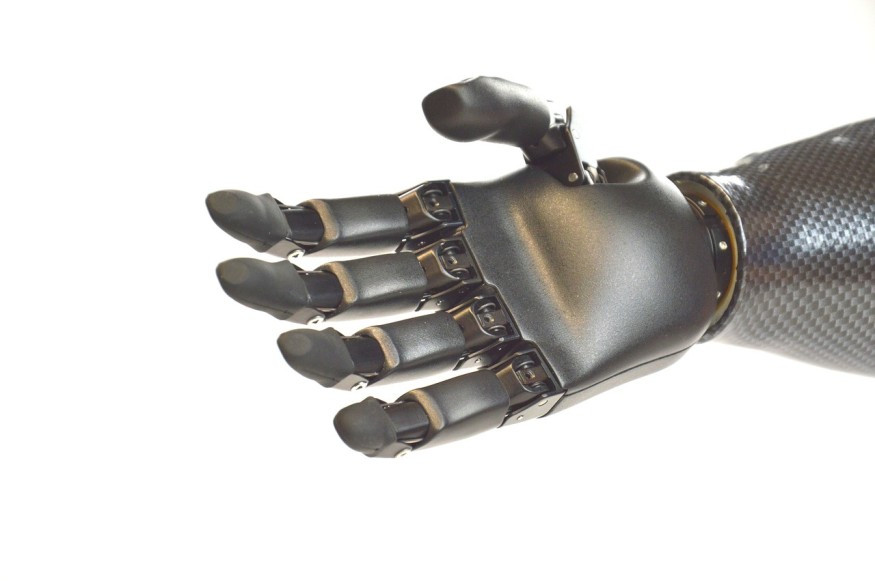
A group of experts have created the most human-like robotic hand ever, complete with 3D-printed bones, ligaments, and tendons.
Need for Human-Like Robotic Systems
It has been a long-standing goal for humanity to recreate synthetic but complex systems which can operate like natural organisms. Such systems are usually designed and controlled through the combination of rigid structures.
Over the recent years, engineers have designed increasingly sophisticated robotic systems which can mimic both the structure and function of the human body, such as the hands. Ideally, robotic hands are expected to perform highly precise movements while also being relatively affordable and easy to fabricate.
However, most bio-inspired skeletal structures for robotic hands have very intricate designs which contain numerous advanced components, making them difficult to fabricate on a large scale. Conventional robots are also not flexible and lack the intricate internal structures required in performing complex movements and tasks that humans can perform easily. Many such devices, like metal implants, are not suited for use in medical contexts because they cause inflammation when the bodies detect the difference between their stiffness and that of the surrounding tissue.
A New Approach in Robot Design
Unlike humans and animals, robots do not possess real bones or the flexible tissues that connect them. Instead, they are made with artificial links and joints made of materials such as carbon fiber and metal tubes. Although these internal structures enable a robot to move, grab objects, and maintain various postures, they are not as flexible, agile, and soft as human bodies.
To address this problem, a group of scientists set about 3D printing various devices which mimic the complexity of nature's biomechanics. Their trial devices include a functional heart pump, a sex-legged robot, and a material that absorbs vibrations from its surroundings. The result of their experiments was discussed in the study "Vision-controlled jetting for composite systems and robots".
In designing their soft robot, the scientists 3D printed the hand using a new technique called slow-curing, where plastics are given more time to set to make them more durable. The experts believe that this 3D printing technology can be used in creating more complex and durable robots.
The researchers also used vision-controlled jetting (VCJ) technique, which involves mixing hard and soft parts by cross-layering up to four plastics. This results in a firm but soft robotic part that can scale, in contrast with other soft robots which struggle to maintain their physical properties at larger sizes.
Unlike fast-curing polyacrylates used in traditional 3D printing, VCJ provides each layer of the robotic part more time to set. The printer was guided with cameras and lasers to make sure that each layer is built up with the correct thickness.
In terms of the material used, the team preferred the slow-curing thiolene polymers since they have very good elastic properties and return to their original state much faster after bending than polyacrylates.
According to ETH Zurich robotics professor Robert Katzschmann, robots made of soft materials have advantages over conventional ones made of metal. Since they are soft, there is less risk of injury when working with humans, and they are also better suited in handling fragile goods.
RELATED ARTICLE : Scientists Design a Robot Hand That Can Segregate Recyclable Waste
Check out more news and information on Robotic Hand in Science Times.