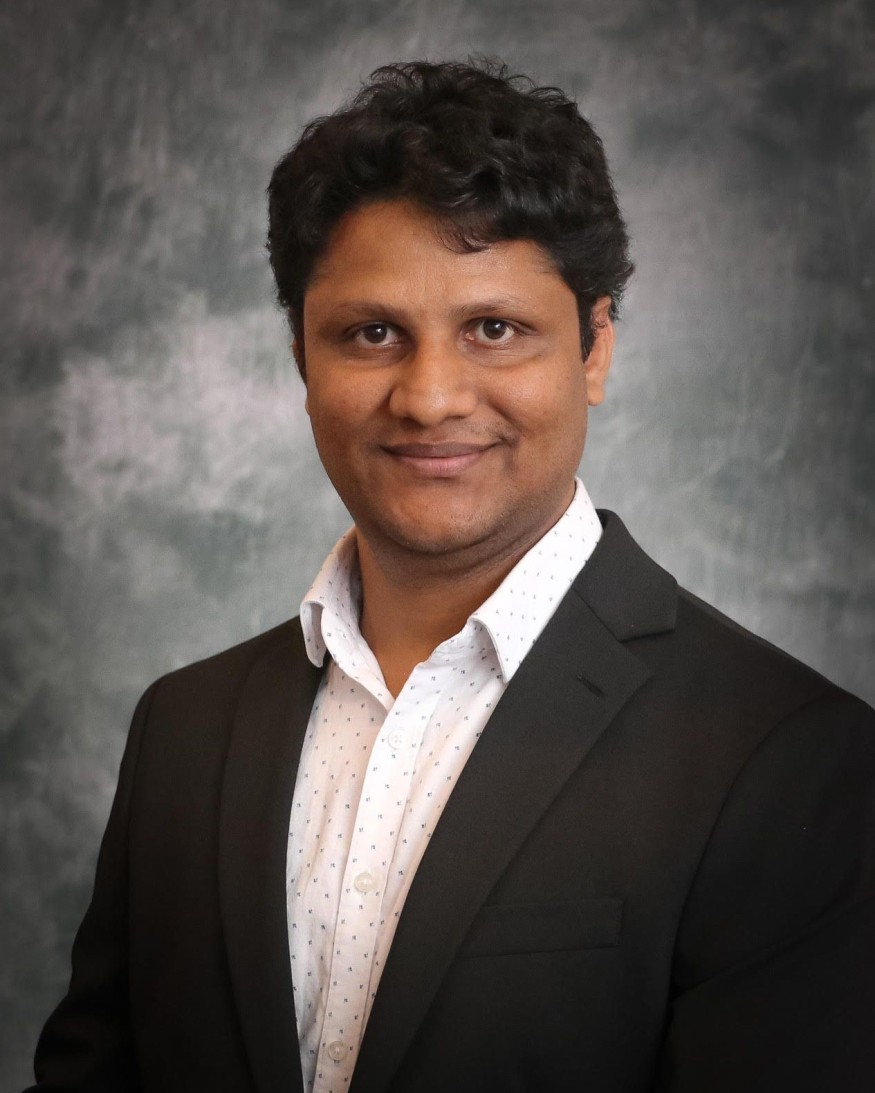
In the dynamic field of aviation engineering, Suresh Bodenpally is recognized as a visionary engineer with a proven track record in repair development, analysis, and certification. Specializing in regulatory compliance, he has collaborated closely with the Federal Aviation Administration (FAA) and the European Union Aviation Safety Agency (EASA), playing a key role in creating certification documents for aircraft maintenance and repair. His expertise in structural analysis engineering, specifically in navigating complex regulatory frameworks, has been instrumental in shaping robust standards for safe and efficient aircraft operations, further solidifying his leadership in aviation safety.
With over 16 years of experience in aerospace engineering, Suresh has worked alongside industry giants such as Boeing, Airbus, and Bombardier, gaining invaluable insights into the challenges of aircraft maintenance and repair. His extensive knowledge of FAA and EASA regulations, paired with his hands-on experience, has earned him recognition as a trusted expert, respected by both manufacturers and regulatory bodies alike.
Suresh credits his early experiences working with some of the industry's top engineers for shaping his approach to problem-solving. "In my career, I've learned that nothing beats hands-on experience. Working side by side with some of the best engineers at Boeing, Airbus, and Bombardier, I quickly realized that true innovation happens when you merge deep knowledge with a willingness to embrace challenges head-on. I also had the privilege of receiving training from industry experts whose invaluable insights expanded my technical skills. Their mentorship not only enhanced my technical abilities but also taught me the importance of critical thinking and adaptability when overcoming complex engineering challenges."
Why are structural repairs so critical in aviation today?
As the aviation industry faces ongoing supply chain challenges and production delays, effective repair solutions for aging fleets have become more critical than ever. Older aircraft continue to play a vital role in meeting global air travel and cargo demands, making timely structural repairs essential for keeping these fleets operational. With commercial airliners often in service for decades, the demand for advanced, safe, and cost-effective repair solutions continues to grow.
Maintaining the structural integrity of aircraft is essential for the safety of both passengers and crew. Even minor damage to key components, such as the fuselage or wings, can significantly impact flight performance and safety. Therefore, prompt and efficient repairs are crucial to preventing potential failures and ensuring the long-term reliability and safety of the aircraft.
"One of the toughest aspects of my job was realizing how much trust airlines, operators, and passengers put into the safety of aircraft. Every repair I design impacts people's lives. It's not just about fixing something; it's about keeping people safe in the air. That responsibility has shaped the way I approach every project."
What innovative advances have you made in aircraft structural repair development?
With extensive experience in designing, analyzing, and certifying complex repairs for major aircraft manufacturers such as Boeing, Airbus, and Bombardier, I have addressed a wide range of structural challenges in critical components like fuselage skins and wing spars. My contributions span various damage scenarios, including accidents, bird strikes, lightning strikes, fatigue cracks, and corrosion.
One of my notable contributions is the development of a specialized repair method focused on enhancing the structural integrity and extending the service life of components under high stress, particularly side-of-body frame fittings. Before this repair method, the industry standard was to completely remove and replace the fittings, resulting in significant aircraft downtime and extended periods of in-service unavailability, which led to operational delays. In contrast, my repair approach provides a more efficient solution, using advanced techniques like blending, spot-facing, and surface-finishing to address issues such as corrosion.
The method is not only more durable but also cost-efficient. Unlike traditional methods, which require frequent maintenance, my approach provides a permanent repair, reducing both maintenance frequency and overall lifecycle costs. It is also scalable, enabling its application across entire fleets, helping airlines maximize the operational life of their aircraft while minimizing costly replacements.
What are the most frequent issues in aircraft structures, and how do they occur?
Two of the most frequent and critical issues in aircraft structures are fatigue cracks and corrosion, both of which pose significant risks to the integrity and safety of the aircraft over time.
Fatigue cracks occur due to the repetitive loading and unloading that aircraft structures experience during each flight. Every takeoff, cruising phase, and landing phase subjects the aircraft to cyclic stress, causing the materials to undergo strain. Over time, these repeated stresses can lead to the initiation of microscopic cracks, often in high-stress regions such as wing spars, fuselage joints, and areas with rivets or fasteners. These cracks grow progressively with each cycle of stress, ultimately threatening the overall strength and performance of the aircraft if not properly addressed. This phenomenon is particularly dangerous because the cracks can remain undetected for extended periods, and their growth can lead to catastrophic failure in critical structural areas.
Corrosion, on the other hand, is a gradual electrochemical process that occurs when metal components interact with moisture, salt, and contaminants from the surrounding environment. Corrosion is particularly prevalent in areas of the aircraft that are exposed to moisture, such as the fuselage, wings, and engine components. This degradation process weakens the metal, making it more susceptible to fatigue and reducing its overall load-bearing capacity. Corrosion can also form in microscopic crevices or joints where moisture or debris accumulates, causing localized damage that can spread over time. The combination of corrosion and fatigue makes these structural issues even more challenging, as the affected areas may lose strength in multiple ways simultaneously.
What are the key considerations when designing a repair for corrosion and fatigue cracks?
When designing a repair for corrosion and fatigue cracks, it is critical to assess first the damage severity and location using advanced diagnostic techniques like Non-Destructive Testing (NDT), which enables precise identification of microcracks or corrosion areas without compromising the structure. The repair material must exhibit material compatibility with the original structure to ensure it can withstand the same cyclic stresses and environmental factors, particularly in high-stress areas. Load redistribution must be carefully considered to prevent the development of new stress concentrations that could lead to additional damage. Furthermore, the repair should include long-term durability by using corrosion-resistant materials and the integration of design features that reduce the potential for crack initiation. Ultimately, the repair design must optimize structural integrity, maintain safety margins, and facilitate ease of future inspections to mitigate the risk of further fatigue or corrosion-related failures.
How do you address future fatigue cracks after repairing a structure?
After repairs, fatigue cracks may still develop due to ongoing stresses. To mitigate this, I use Finite Element Analysis (FEA) to model stress distribution and predict potential crack propagation. This helps identify at-risk areas and informs repair strategies that enhance both immediate strength and long-term durability. Additionally, I recommend optimal inspection intervals for operators and integrate non-destructive testing (NDT) techniques such as ultrasonic testing and eddy current inspections to monitor critical areas. These methods ensure early detection of emerging cracks, maintaining the long-term integrity and safety of the aircraft.
Why is FAA and EASA compliance critical for aging aircraft?
FAA and EASA regulations are vital for ensuring the safety and operational reliability of aging aircraft. These regulatory bodies provide a structured framework for repairs, inspections, and modifications, which is particularly crucial for older fleets. As an engineer with extensive experience in aircraft repairs, I ensure that all solutions I design adhere to these regulations, maintaining both the safety and airworthiness of the aircraft.
Aging aircraft face unique challenges, such as fatigue, corrosion, and structural degradation. FAA and EASA standards address these issues by specifying detailed repair procedures, testing methods, and certification requirements to uphold safety. Non-compliance with these regulations can compromise safety, delay operations, and lead to significant financial penalties. My expertise in navigating these complex requirements guarantees that every repair I implement not only resolves the structural issues but is fully aligned with the stringent safety standards set by FAA and EASA, ensuring the continued operational integrity of the fleet.
In addition to your professional work, how else do you contribute to advancing the aviation industry?
Apart from my professional work, I am actively engaged in shaping the future of the aviation industry by contributing to key committees that set industry standards and best practices. As a senior member of the American Institute of Aeronautics and Astronautics (AIAA), I serve on the Committee on Standards (CoS) for Aerospace Design and Structures. Here, I collaborate with experts to develop and update standards that govern aerospace design and analysis.
I am also involved with SAE International, where I contribute to the Standards Committee for A-21 Aircraft Noise Measurement and Aviation Emission Modeling. These efforts are crucial for minimizing aviation's environmental impact and promoting sustainability, ensuring that repairs and modifications comply with evolving environmental and safety regulations.
Additionally, I am a member of the American Society of Mechanical Engineers (ASME), where I participate in the Aerospace & Advanced Engineering Drawings (AED) Standards Committee. In this role, I help develop advanced aerospace drawing standards.
Through these roles, I am directly involved in shaping the technical, regulatory, and safety frameworks that will guide the future of aviation. My contributions influence both national and international standards, enhancing safety, efficiency, and sustainability across the industry. By driving advancements in aerospace design, performance analysis, structural resilience, and eco-friendly practices, I am committed to ensuring that the aviation sector evolves in a way that prioritizes both safety and sustainability for the future.
With the rapid advancements in materials and repair techniques, what do you see as the future of aircraft structural repairs?
The future of aircraft repairs will be largely driven by advancements in materials technology and repair methodologies. As aircraft fleets age, the demand for more efficient and effective repair techniques that extend service life while maintaining safety will only increase. We're seeing exciting developments in advanced composite materials, along with stronger, more durable metals and coatings that will improve the ability to repair critical structural components. Additionally, the evolution of non-destructive testing (NDT) methods will allow for more precise detection of issues such as micro-cracks and corrosion in hard-to-reach areas.
However, the integration of these sophisticated techniques into existing maintenance programs while maintaining compliance with strict regulatory standards will present a challenge. Moreover, balancing cost-effective solutions with the rigorous safety standards mandated by authorities like the FAA and EASA will be critical. In my opinion, overcoming these challenges will require a combination of innovative repair techniques, robust training programs, and a long-term commitment to ensuring aircraft reliability and safety.
Conclusion
Suresh Bodenpally's groundbreaking work in aircraft structural repair and safety has not only addressed the pressing challenges of maintaining aging fleets but also set the stage for the future of aviation. As the industry moves toward more sustainable practices, the repair methods, materials, and lifecycle cost efficiencies he has pioneered are poised to play a key role in reducing aviation's environmental impact. By extending the service life of existing aircraft, his work minimizes the need for new manufacturing, reducing waste and conserving valuable resources.
Looking ahead, Suresh's contributions are likely to influence the next generation of aircraft design. The integration of advanced materials and repair techniques will likely lead to lighter, more durable airframes that require less frequent maintenance. Furthermore, as sustainability becomes an even greater focus, his expertise in ensuring that aircraft meet the highest safety standards will be instrumental in helping manufacturers design aircraft that are both environmentally responsible and economically viable. Through his innovative solutions and unwavering commitment to safety, Suresh Bodenpally is not just addressing today's challenges—he is laying the groundwork for a safer, more sustainable future in aviation.