Using simple physics, researchers at Princeton University were able to develop and grow artificial hair. Specifically, they are able to transform an old series of engineering conflicts into a manufacturing solution.
According to an Interesting Engineering report, nature has abundant patterns leading to nonstop far-from-equilibrium process, as well as systems that are rich when it comes to diversity and complexity.
Essentially, their evolving conditions make examining, modeling and translating them to engineering a struggle. In connection to this development, the researchers, inspired by both biological and nature designs, have rationalized such an inspiration with mathematical precision and come up with a relatively simpler system that allows them to coat a liquid on a disc's external part, and spin it to form complicated patterns, a press release specified.
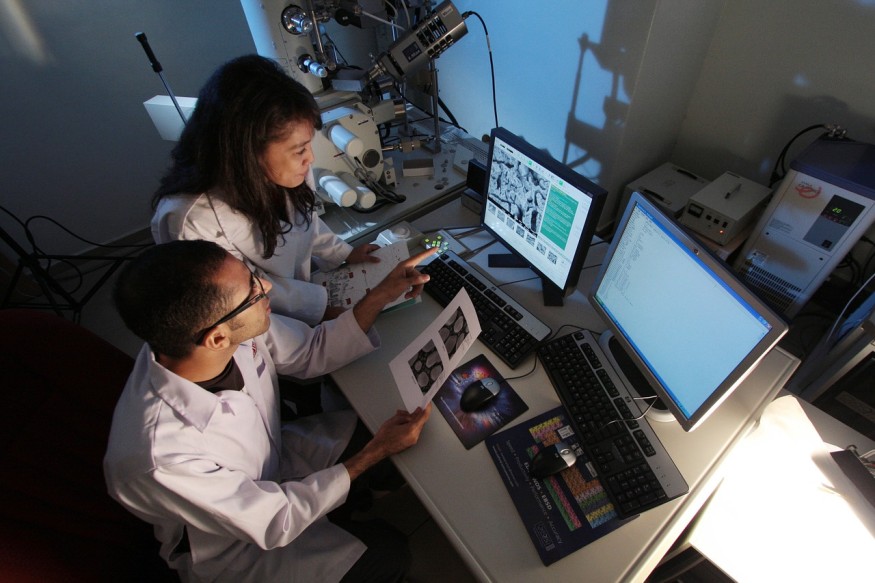
The Spinning Technique
Tiny spindles ascend from the material as it cures after it receives the proper spin and grows as the disk speeds up.
This spinning technique of the elastic polymers allowed researchers to form the kinds of complicated shapes akin to hair, needed for the creation of biomimetic surfaces.
According to chemical and biological engineering assistant professor Pierre-Thomas Brun, from the Princeton, such patterns are universal in nature.
This assistant professor, who's also the study's principal investigator added, in their study which the Proceedings of the National Academy of Sciences published, their approach is leveraging the way such structures are forming naturally
'Fluidic Instability'
This system is combining a fluidic instability and enormous solid deformation in hardening melts for the production of soft solids with multifaceted surface geometry.
Such a procedure is set on simple physics although, as earlier mentioned, it's turning an old set of engineering issues into a new solution for manufacturing.
The study investigators wrote in their study that this simple approach is simple, affordable, and more sophisticated compared to the conventional molds and that it could play a vital role in the development of robotic sensing capabilities.
It is applicable to an extensive range of problems where numeric deformations, as well as solidification are said to be connected or associated.
In the middle of a shift toward additive manufacturing, this could be considered a major part of the revolution by giving way to the use of multiple steps of moldless approaches of the formation of multifaceted substances.
Co-authoring this paper are Princeton postdoctoral researcher, Etienne Jambon-Pauillet; and Matthieu Royer Piechaud, who's formerly associated with Princeton.
This particular research was partly financially backed by a National Science Foundation grant through the Princeton Center for Complex Materials.
Robotic-Sensing Capability
Robotic-sensing, as shown in Yantra Parignan's YouTube video below, is robotic science's subarea intended to provide the robots with sensing capabilities so that they are more human-like. In addition, this capability primarily gives the robot the ability to touch, hear, move and see, not to mention, uses processes that necessitate environmental feedback.
In addition, robotic sensors are used to approximate the condition and environment of a robot. Such sensors are transferred to the controller to allow the proper or suitable behavior to take place.
The sensors in robots are grounded on the human sensory organs' functions. Lastly, robots need the extensive information about their surroundings so they can function more effectively.
Read also: New Study Finding: Autism Is Thrice More Common in Boys, and Vitamin D Has Something To Do With It
Check out more news and information on Physics in Science Times.