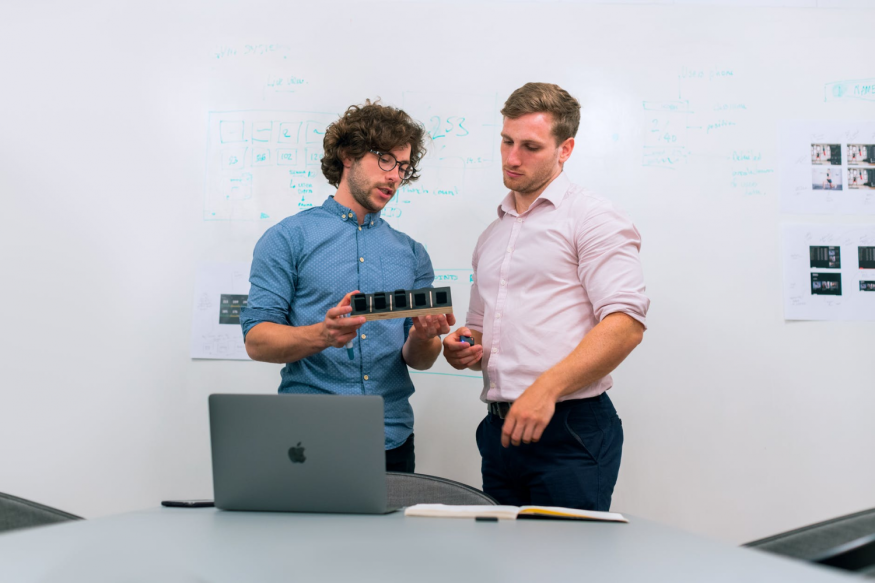
Investment casting is a staple in the world of innovation and design. It's one of the most common processes used for its precision, simplicity, and versatility. For those entering the manufacturing industry, having a baseline understanding of investment casting is a must.
Here is what you need to know about investment casting, its advantages and disadvantages, and how it's used.
What Is Investment Casting?
Investment casting is a process through which a pattern or mold is covered in a ceramic slurry, then used to shape molten metal into a desired form. This process is often referred to as "lost wax casting," as the ceramic slurry is traditionally poured over a wax master pattern. The wax is then melted out of the ceramic mold before the molten metal is poured in.
The investment casting process has evolved over the years, with many manufacturers opting for 3D printed investment castings to save time and money, especially when crafting more complex molds. This approach is also ideal for companies running smaller productions or facing reduced timelines.
What Is Investment Casting Used For?
Investment castings are used in a variety of industries. Two of the most notable areas are the aerospace and firearms industry - both of which, of course, carry over into military projects.
In aerospace, investment castings are used to mold alloys into engine components, such as propellers or turbine blades. This process is incredibly nuanced, as natural metals are too soft to be used in aerospace parts, and the alloys must be free of defects that could ultimately cause a loss of life.
Regarding firearms, manufacturers use investment casting to create the many smaller pieces that make a firearm operational. These pieces could include anything from the hammer to the trigger. Again, creating precision, defect-free pieces is essential to prevent malfunctions when operating the weapon.
Though aerospace and firearm manufacturing are two notable industries that use investment casting, there are also processes in the automotive industry, food service, and anything that requires small, precision mechanics.
How Investment Casting Works
In the traditional investment casting process, a wax pattern is designed around which to create a mold. The wax core is often referred to as the "master plan" and can be costly and time-consuming to get just right, which is why many companies have shifted to 3D printed patterns.
The wax pattern is then coated in a ceramic slurry that's made to withstand high heat. From there, the internal pattern is burned out of the hardened ceramic slurry mold. If this process is done incorrectly, the mold will be useless as it will create defects in the parts.
The molten metal or alloy is then poured into the ceramic mold, sometimes at temperatures exceeding 3000 degrees Celsius, and allowed to cool and harden. While some molds are gravity-fed, others must be moved or vented to allow for thinner or more complex designs.
When the metal has hardened, the ceramic mold will be removed, making the finished prototype or piece ready for inspection.
Advantages of Investment Casting
One of the primary advantages of investment casting is that it creates a smoother finish compared to other methods, such as sand casting. Investment casting also offers a lot of versatility and precision work, especially when 3D printing is utilized.
Disadvantages of Investment Casting
The pitfall of investment casting is that it can be costly and is often limited to smaller batch production runs of less than 10,000 parts. There are also limitations around sizing and precision, though the shift toward 3D printing has helped.
Understanding the steps involved in investment casting can help innovators and new engineers create sustainable workflows that result in high-quality, precision parts.