Army-funded researchers from the Massachusetts Institute of Technology (MIT), California Institute of Technology (Caltech), and ETH Zurich showcased a nanoarchitected material designed from nanoscale patterns better than Kevlar or steel material for making lightweight armor for future soldiers.
The nanoarchitected material was tested in the Army-sponsored research center Institute for Soldier Nanotechnologies (ISN) in the MIT, which showed that it could withstand impacts from microparticles at a supersonic speed.
This could be a promising new material for making lightweight armor, protective coatings, and other impact-resistant materials for the Army. They published the findings of their study, titled "Supersonic impact resilience of nanoarchitected carbon," in the journal Nature Materials.
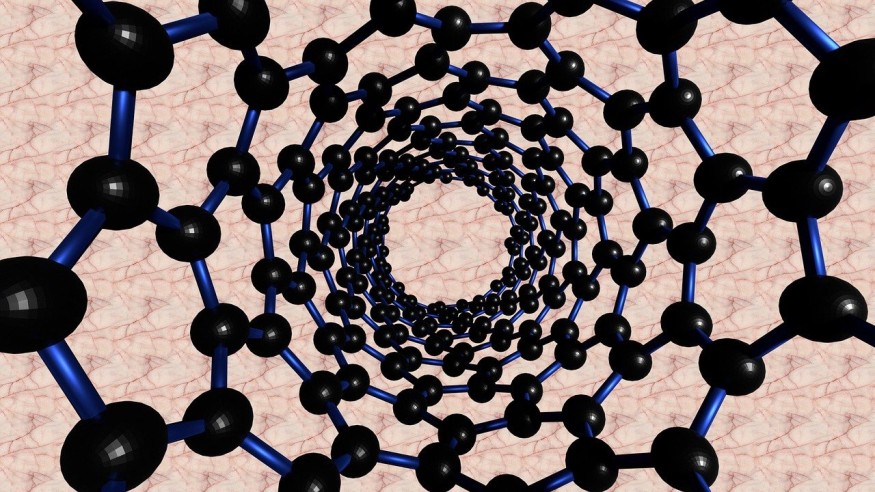
Ultralight Nano-Built Material Can Withstand Supersonic Microparticle Impacts
Dr. James Burgess, ISN program manager, told Army Times that the lightweight material had been tested in a laboratory, and results suggest that it could take on supersonic impacts and may work better than the traditional materials used for armors or protective materials because it has more layers at a nanometer scale.
Dr. Burgess tried to compare it with a motorcycle helmet to explain its protective process. He said that if a helmet shell that can take on a high impact before it breaks is contained in tiny layers, it will provide even greater resistance that cannot be observed in steel or even Kevlar.
According to Science Daily, the nanometer-scale carbon struts give the material its toughness and mechanical robustness. The team has tested the material when they shoot it with microparticles at supersonic speeds and found that the lightweight material that is as thin as human hair had prevented the microparticles from penetrating it.
Moreover, Dr. Carlos Potela shared with Army Times that the lightweight material known as photoresist conforms its shape based on light exposure. Technically, it is like 3D printing using a tightly focused laser at the nanoscale to solidify the material until it is fully printed.
The key to making the nanoarchitected material is to allow designers to create any imaginable 3D shape that is stiffer and stronger than the traditional manufacturing methods. They hope to create protective materials that are ultralight but at the same time could provide even greater protection for future soldiers.
ALSO READ : High-Density Glass From a New Type of Thin Film Liquid Could Create Stronger, Denser Materials
How Did the Nanoarchitected Material Survive Supersonic Impacts?
The team wanted to know how the nanoarchitected material survived supersonic impacts during the testing. Caltech's news release reported that Portela constructed the material from the photosensitive polymer using two-photon lithography. Then, he burnt them in a furnace in a process called pyrolysis at an ultra-high temperature to convert the polymer into pyrolytic carbon.
The team created a denser and a looser version of the material to test any differences. They then blasted both materials with microparticles at supersonic speeds, at an average speed of sound that is about 340 meters per second.
They found that the denser version was more resilient as it embedded in the material rather than penetrating it. A close examination of what happened revealed that the nanometer-scale carbon struts surrounded the particle but remained intact until the projectile stopped, unlike a fully dense material, outperforming steel and Kevlar by 70%.
Now they have to find ways to scale it up and explore how other nanoarhitected materials could hold up under supersonic impacts so that they could be used in real-world applications.
RELATED ARTICLE : New Bacteria-Based Fiber Tougher, Stronger Than Natural Spider Silks
Check out more news and information on Nanotechnology in Science Times.