In a breakthrough in the field of 3D printing, scientists from the University of New South Wales (UNSW) have developed a way for 3D-printed plastic to effectively 'heal itself' quickly and cheaply. They added a special powder to the liquid resin used in 3D printing and found that it could help repair the damaged part of the material.
The repairs could be done at room temperature under LED lighting, which will activate the chemical reaction and fuse the fractured pieces. According to Australian Associated Press, it is a different method from current technology. Disassembled products are put through a series of heating cycles that require 24 hours to complete compared to only an hour in the new method.
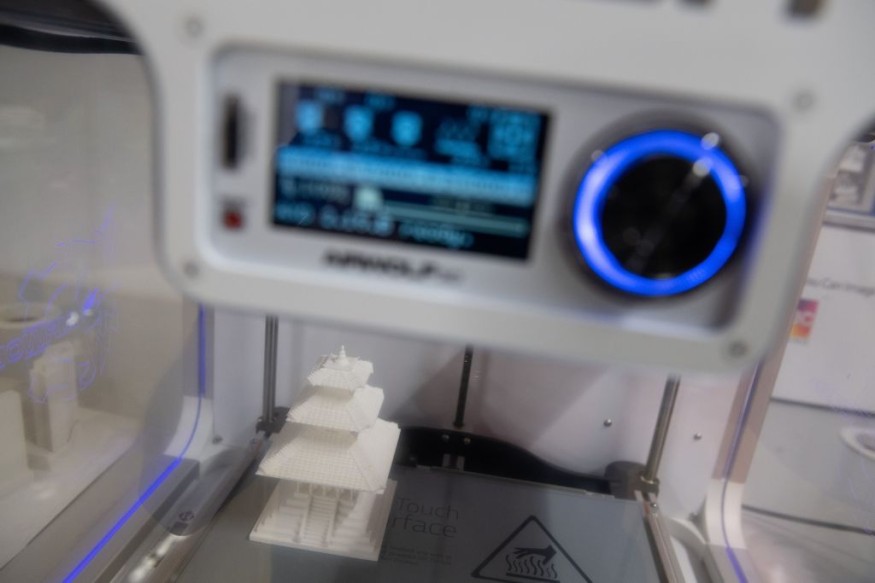
Previous Way of Repair Damaged 3D-Printed Plastics
Sometimes 3D printing might not be successful in which some parts end up broken due to weak points in the models, which is avoidable but also can be fixed. According to an article in 3D Printly, fixing damaged 3D-printed plastic parts involve using epoxy or super glue to glue the pieces together or using a hot gun to melt materials to rejoin them and bind the pieces together.
The solution of repairing damaged parts usually depends on the situation because one solution may not solve the problem, or perhaps it could be easier to solve when using other methods.
But to best repair, the damaged part, first prepare a flat and stable surface where the fixing will be done and then gather all the 3D-printed parts and the adhesive needed, like the superglue or epoxy. Before applying the glue, make sure to sand down the pieces to remove rough pieces that may get in the way of binding the pieces together.
Then apply a small amount of the adhesive to the main part and connect the broken or damaged 3D-printed part. Hold it together for at least 20 seconds to create a bond. After that, place the object down and let it cure.
New Way of Repairing 3D-Printed Plastic Can Also Reduce Waste
The previous method of fixing damaged 3D-printed parts takes longer than the new method developed by scientists from UNSW. In the study, titled "A Photoinduced Dual-Wavelength Approach for 3D Printing and Self-Healing of Thermosetting Materials," published in the journal Angewandte Chemie International Edition, they demonstrated an easier and quicker way to repair damaged parts.
Moreover, Phys.org reported that this method would prevent delays that usually involve extra time, money, and waste. Dr. Nathan Corrigan, the team's spokesperson, said that this method allows for easier repair in many situations damaged parts and salvage them instead of being thrown out and starting again from the beginning.
Dr. Corrigan also noted the environmental impact of this new method, stating that re-synthesizing a material will increase its lifespan and reduce plastic waste.
How Did They Repair Damaged Plastics so Fast?
To do this, they used the powdered additive trithiocarbonate or also known as a reversible addition-fragmentation chain transfer (RAFT) agent that CSIRO originally developed. Mail Online reported that it targets the nanoscopic network of the elements to allow binding of broken parts. This can be done under UV LED lights for 30 minutes.
In the experiment, which involved a 3D-printed violin, researchers demonstrated its self-repair capabilities and showed its strength is fully recovered compared to its previously unbroken state. The team noted that this method could be commercialized given the simplification and speed of the system used compared to previous methods of repairing damaged 3D-printed plastic.
Professor Cyrille Boyer said that the new method also could be used in various applications where advanced 3D materials are being used, especially in high-tech industries that provide specialized components.
Check out more news and information on 3D Printing in Science Times.