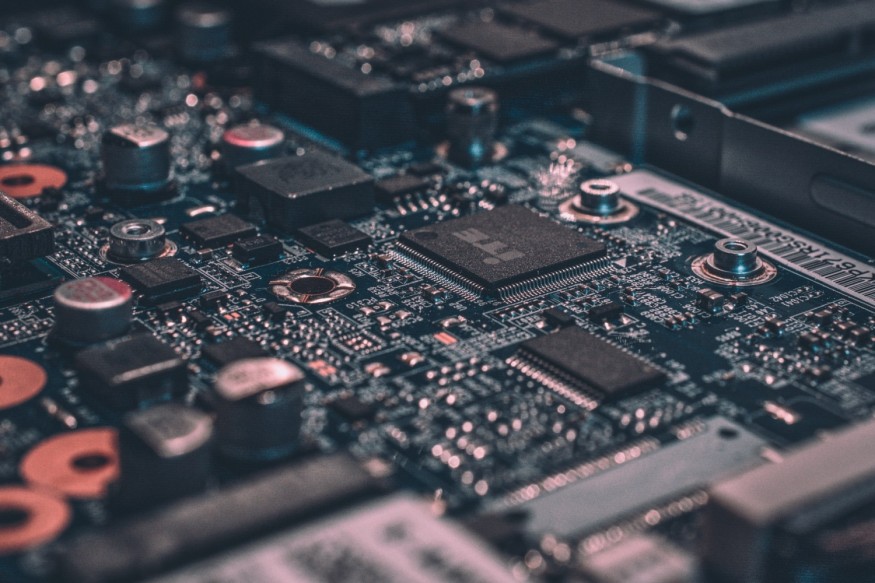
With rapid advancement in the electronics industry, the global technological landscape keeps revolving. The need to control costs continues to be a major driving force for manufacturers, with new technologies emerging in the market providing revenue opportunities but requiring manufacturers to initiate partnership with technology solutions providers and other organizations that can supply expertise outside of the company's core focus. Every trend comes along with challenges, the recent nature of electronics manufacturing trends is no exception. The primary target of electronics manufacturers is to find ways to capitalize on current trends. Their secondary priority is to control costs, integrate technologies outside of their primary areas of expertise, and meet customer demands for more efficient, eco-friendly manufacturing processes and electronics.
Electronics manufacturing industry is facing few challenges along with some opportunities as well. To catch up with competition it is indeed necessary to remain relevant and updated about recent designing trends in the electronics industry. Therefore, an electronics company needs to be both flexible and quick. Hence, to emerge as a successful company, one must be able to overcome both existing and emerging challenges in the market. Here are five of the major challenges faced by the electronics manufacturing industry.
Increasing Demand for Smart Electronics Devices:
Smartphone and smart device's market have rapidly grown for the last two decades. With each generation of updates, smart devices are getting smaller and smaller, which require electronics manufacturers to adopt advanced nanotechnology in their manufacturing process to keep up with trends.
To assemble micro components, manufacturing companies adopt micro dispensing technologies, which require a precise amount of adhesive and silicones. Shortage of such material can be proven troublesome for the manufacturing industry, which has recently occurred due to the global pandemic caused by COVID outbreak.
Sustainability:
As the awareness for being green is increasing, pressure is mounting upon manufacturers to keep coming up with new technologies and products which are more energy efficient and sustainable. Factors like carbon top and carbon exchanging have become more important than ever in green electronics manufacturing.
As climate change continues to mount, there is increasing pressure from consumers, businesses, and governments to adopt eco-friendly manufacturing solutions. Hence manufactures are required to qualify for ISO certification or similar, to boost their public image.
Short Product Life Cycle:
Economic volatility and cyclical demand altogether cause fluctuations in production. Due to ever changing trends in the electronics industry and fluctuating demands, it is incredibly difficult for electronics manufacturers to accurately predict and maintain production goals. Hence, it requires efficient lean capabilities to maintain inventory as per demand.
Complex Global Supply-chain:
More and more, companies are having to juggle internal and external resources while maintaining crucial international standards. Operational burdens are increasing due to factors such as traceability and compliance. Nowadays, it has become common practice in western countries to import electronic components or sub-components from Asian countries.
Service and Warranty Management:
Leveraging the global supply-chain is putting more focus on supplier quality management. It goes without saying that an increasing global market significantly raises efforts in maintaining after-sales service. Having a strong quality and traceability system directly impacts warranty reserve and post-production service hours.