The Romans were skilled in construction and engineering, particularly demonstrated in their aqueducts. These structures are made with a special type of concrete called pozzolanic concrete, which has excellent durability and gave Roman buildings their impressive strength. The Pantheon, a structure that is still standing after almost 2,000 years, is made of unreinforced concrete and has the distinction of being the world's largest dome made of this material.
Previously, it was believed that the strength of pozzolanic concrete was due to the use of a specific type of volcanic ash called pozzolana and lime, which when mixed with water, create a block of strong concrete. However, recent research from a team at MIT has revealed that the ingredients and mixing techniques used for this type of concrete may have been different than previously thought.
According to materials scientist Admir Masic of MIT, small white chunks of lime found in seemingly well-mixed pozzolanic concrete had previously been attributed to poor mixing or inferior materials. However, Masic was skeptical of this explanation, stating that the idea that the presence of present lime clasts was simply attributed to low-quality control always bothered him.
'Hot-Mixing Process'
MIT's Admir Masic and Linda Seymour led a team that studied 2000-year-old samples of Roman concrete from the Privernum archaeological site in Italy. The researchers used a variety of techniques including large-area scanning electron microscopy, energy-dispersive x-ray spectroscopy, powder X-ray diffraction, and confocal Raman imaging to examine small white chunks of lime found in the concrete. The team was puzzled by the presence of these chunks, as it seemed unlikely that the Romans would have used poor quality materials or production techniques given the importance they placed on creating strong concrete, following a report from ScienceAlert.
The researchers were also interested in understanding the type of lime used in pozzolanic concrete. Traditionally, it was thought that the Romans used a type of lime called slaked lime, which is made by mixing quicklime (calcium oxide) with water. However, the team's analysis of the lime chunks in their samples showed that Roman concrete may have been made by combining quicklime with pozzolana and water at high temperatures, either alone or with slaked lime. This process, which the team refers to as "hot mixing," resulted in the formation of the lime clasts.
Masic explained that the "hot mixing" process used by the Romans had several advantages. Firstly, it allowed for the formation of high-temperature-associated compounds that cannot be produced using slaked lime alone. Secondly, the high temperatures used in this process significantly reduced the curing and setting times of the concrete, enabling faster construction.
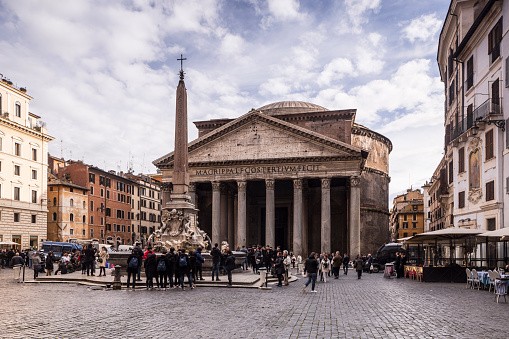
Ancient Works Standing in Present
In addition to its other benefits, the presence of lime clasts in pozzolanic concrete gives the material self-healing properties. When cracks form in the concrete, they tend to travel to the lime clasts, which have a larger surface area than other particles in the mixture. When water enters the crack, it reacts with the lime to form a solution high in calcium that hardens as it dries, forming calcium carbonate and sealing the crack.
This process has been observed in concrete from the Tomb of Caecilia Metella, a 2000-year-old site, where cracks in the concrete were filled with calcite. It may also explain why Roman concrete from seawalls built 2000 years ago has remained intact despite being exposed to the ocean's constant waves. To test their theory, the team made pozzolanic concrete using ancient and modern recipes that included quicklime, as well as a control concrete without quicklime, and performed crack tests. The results showed that the quicklime concrete was fully healed within two weeks, while the control concrete remained cracked.
The MIT team is now working on developing a commercial version of their environmentally friendly concrete as an alternative to current concrete. Masic believes that this more durable concrete could improve the service life of traditional materials and be used in 3D-printed concrete formulations. The research analysis was reported in the journal Science Advances.
RELATED ARTICLE : Ancient Constantinople Aqueduct a Solution to Clean Water Systems
Check out more news and information on Archeology on Science Times.