A new catalyst developed by researchers converts hydrocarbons into chemicals and materials with higher value, which are also simpler to recycle and biodegrade in the environment. This catalyst transforms substances like motor oil, the plastic found in single-use grocery bags, the caps on water or milk bottles, and even natural gas. Ames National Laboratory scientist Aaron Sadow, who also serves as director of the Institute for Cooperative Upcycling of Plastic (iCOUP) and a professor of chemistry at Iowa State University, led the group of researchers who created it.
The purpose of the new catalyst is to give aliphatic hydrocarbons functional groups. Only carbon and hydrogen make up aliphatic hydrocarbons, which are organic substances. In most cases, they do not mix with water, but rather form distinct layers, in part because they do not contain functional groups. Functional groups are particular clusters of atoms within molecules that have particular properties. These hydrocarbon chains' properties can be significantly altered by the addition of functional groups, making the materials recyclable.
Producing Hydrocarbon to Chemicals
The only hydrocarbon in natural gas that consists solely of carbon-hydrogen (CH) bonds is methane. Carbon-carbon (CC) bonds hold carbon atom chains made up of oils and polymers together, according to Sadow. A large portion of crude oil and refined petroleum products like plastics and motor oils are made up of aliphatic hydrocarbons. These materials lack other functional groups, which makes them difficult to biodegrade, according to Sadow. To take these kinds of materials and add other atoms, like oxygen, or to create new structures from these simple chemicals has thus long been a goal in the field of catalysis.
Regrettably, the traditional method of atom addition to hydrocarbon chains requires significant energy inputs. First, small building blocks of petroleum are "cracked" by heat and pressure. Then chains are grown using those building blocks. The desired atoms are then finally added to the chains' ends. With this novel method, existing aliphatic hydrocarbons are converted instantly at low temperatures without cracking. The results of this study are further discussed in the article "Zirconium-Catalyzed C-H Alumination of Polyolefins, Paraffins, and Methane," which was published in the Journal of the American Chemical Society (JACS). The work was also highlighted in the JACS Spotlight article "A Versatile New Tool for Making Commodity Chemicals."
In a previous experiment, Sadow's team attached aluminum to the ends of the smaller chains while using a catalyst to break the CC bonds in these hydrocarbon chains. Then, functional groups were introduced by adding oxygen or other atoms. The team discovered a way to omit the CC bond-breaking step to create a complementary process. The team might need to shorten chains or add the oxygen functional group, depending on the starting material's chain length and the desired properties of the finished product, Sadow said. The chains from the catalyst could theoretically be transferred to aluminum and added air to install the functional group if they could prevent the CC cleavage.
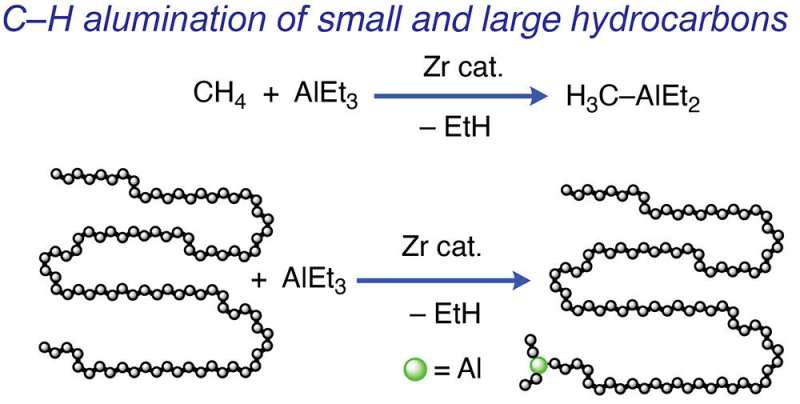
ALSO READ : Gas Flares Producing Five Times Methane Versus Hydrocarbon, Causing Climate Problems, Study Finds
Team Science Advantages
According to Sadow, a commercially available zirconium compound is attached to a silica-alumina material to create the catalyst. The materials are all inexpensive and readily available on Earth, which is advantageous for potential future commercial applications. The catalyst and reactant also have advantages in terms of cost and sustainability. The most common metal on Earth is aluminum, and the aluminum reactant used in its synthesis does not produce any unwanted by-products. The precursor zirconium alkoxide-based catalyst is air-stable, easily accessible, and reactor-activated. So this catalyst precursor is manageable, unlike a lot of early organometallic chemistry that is very air sensitive, according to Sadow.
Phys reported that with the help of this chemistry, it will be possible to modify the physical characteristics of various plastics, such as making them more durable and customizable. They anticipate being able to incorporate more and more functional groups as they further develop the catalysis to modify the physical characteristics of the polymers, according to Sadow.
The collaborative nature of iCOUP, according to Sadow, is what made this project successful. Using Nuclear Magnetic Resonance (NMR) spectroscopy, Perras' team at Ames National Laboratory investigated catalyst structures. Researchers from Cornell University and Argonne National Laboratory, led by Coates, LaPointe, and Delferro, examined the structure and physical characteristics of polymers. Additionally, the University of Illinois' Peters group statistically modeled polymer functionalization. The center's project successes, according to Sadow, "build on contributions of many groups' expertise, and added that the work demonstrates the advantages of team science.
RELATED ARTICLE: Novel Catalyst Can Turn Carbon Dioxide Into Gasoline 1,000 Times More Efficiently Than Existing Methods
Check out more news and information on Hydrocarbons in Science Times.
© 2025 ScienceTimes.com All rights reserved. Do not reproduce without permission. The window to the world of Science Times.