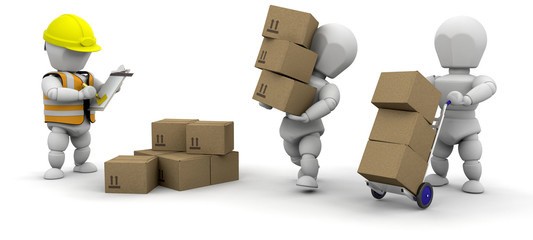
Every logistics and production endeavor relies heavily on material handling systems since they are essential in almost every operation, from manufacturing and storage to shipping and disposal.
Primarily, material handling systems are categorized into two types: Manual and automated. But how to figure out which one would be the best fit for your business?
Here is an extensive guide that covers the two prominent material handling systems along with their pros & cons to assist you in deciding which one would serve your business the best. Let's dig deeper.
Manual Material Handling (MMH) Systems
In Manual Material Handling (MMH), the products and goods are physically moved, lifted, retrieved, and stored by humans (or, in some cases, animals too).
Although manual, this type of material handling also involves utilizing types of equipment such as the following:
Pallet trucks
Manual cranes
Short-distance conveyors
Forklifts
Slings and hooks, etc.
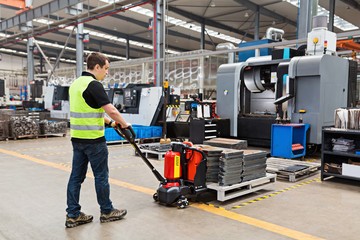
Top Benefits Offered by a Manual Material Handling System
Cost-effective- There is little in the way of up-front costs. Since there is a small outlay of capital, the realization of the payoff is almost instant.
Enhanced process efficiency- Dynamic procedures in which parameters are regularly altered can be finished quickly and efficiently by involving trained and skilled workers.
Easy to adapt- The lack of technical knowledge required to operate this system makes it simpler for personnel to adjust to the new setting.
Cons of Employing a Manual Material Handling System
Scalability issues- Manual handling can't keep up with the demand of a rapidly expanding business that needs to manage an increasing number of operations simultaneously.
Error-prone- This handling type is inaccurate and susceptible to errors since it requires human participation. Possible areas of failure include stock management and order-filling procedures.
Compulsory safety training requirement- Employees must participate in mandatory safety training to ensure that they can safely operate any equipment, such as a milling machine, and related tasks.
Automated Material Handling (AMH) Systems
Automated Material Handling (AMH) implicates the utilization of robots and other digital, programmed devices for the purpose of transporting, pulling, lifting, dropping, pushing, storing, and fetching commodities and products.
Check-in tools, conveyors, elevators, stackers, offloading machines, containers, bins, carts, and tote carriers are only some of the mechanical equipment that could be employed in an AMH system.
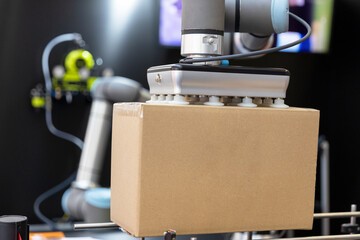
Top Benefits Offered by AMH Systems
Highly cost-efficient- Substantial cost savings could be realized by using an automated system over the long term. The technology might cost a lot initially. However, the savings in labor time will sufficiently make up for the initial investment. Due to automation, operations can be executed more quickly and accurately, which boosts output.
Better order fulfillment and delivery- Automated order processing reduces human error, boosts efficiency, and speeds up shipment and delivery, leading to a better customer service experience.
Superior workplace safety- In addition to reducing the likelihood of slips and trips, AMH eliminates the need for workers to handle or transport heavy loads. Lower back discomfort, back injury, and weariness are all things that are less likely to occur.
Improved space optimization- It's possible to make the most of the available space. Automated equipment like forklifts can help access spaces at great heights, increasing space to stack products. Additionally, an AMH system makes product retrieval much quicker and less labor-intensive. More room is created, which efficiently uses the available space.
Some Drawbacks of Employing AMH Systems
High up-front investment requirement- The initial investment in automated equipment is greater than the investment in manual machinery. This could act as a barrier for low-budget businesses.
Potential downtime due to malfunction- There is a frequent risk of malfunction or breakdown with automated systems, which can result in significant downtime while it gets serviced.
Which Material Handling System Is Better for Your Business?
There are benefits and drawbacks to both types of material handling systems. To decide between a manual and an automated system, you need to consider your budget constraints as well as the volume of your current and projected material handling needs. If your current volume is minimal and not expected to increase in the near future, upgrading may be a costly decision.
However, if you ultimately decide to enhance automation, you can test it on a smaller scale first. For instance, incorporating a few sophisticated systems into your assembly line allows you to tweak your current manual material handling system. If this small-scale experiment goes well, you can implement this adjustment system-wide.
Since it'll take a long time for you to see a return on your investment, it's imperative that you make an informed decision based on reliable data and business demand projections.
Conclusion
Despite the growing interest in automated material handling technologies, many businesses still rely on time-tested manual handling approaches. However, many factories and warehouses have found that a hybrid system combining automatic and manual processes is the best fit for their operations. It is, therefore, up to you to make the ultimate choice keeping your business interests in mind.
.
About the Author:

Peter Jacobs is the Senior Director of Marketing at CNC Masters. He is actively involved in manufacturing processes and regularly contributes his insights for various blogs in CNC machining, 3D printing, rapid tooling, injection molding, metal casting, and manufacturing in general.