Exploring the deep regions of the Solar System will be impossible without the massive use of robots that will be used to build and maintain bases. However, sending a small mass of materials to other planets can cost millions. Because of this, NASA plans to construct highly advanced materials to help skip almost all the weight.
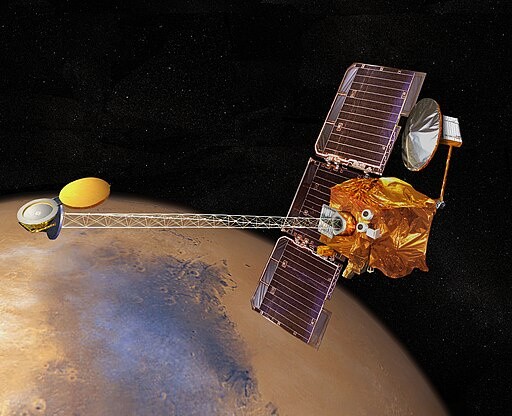
Zero Mass Space Exploration
In the 1940s, John von Neumann proposed the concept of zero mass exploration, which is rooted in self-replicating machines. Self-reprogrammable metamaterials refer to materials that do not exist in nature but can change their configuration independently. It is an idea that the engineering system can replicate and sustain itself in the environment.
Robert A. Freitas Jr. proposed a self-replicating interstellar spacecraft from this concept in the 1980s. Called the Von Neumann probe, this vehicle would visit a nearby star system, find resources to build a copy of itself and send it to another stellar system.
However, the Von Neumann probes would face challenges to take elements from the soil of an alien world and process them into actual engineering components. Doing so would be resource-intensive and would require huge amounts of energy.
Ultra-Lightweight Building Blocks
This problem is exactly what the experts at NASA Ames Research Center and Stanford University are testing with algorithms, robots, and highly advanced building materials. The details of their study are discussed in the paper "Ultralight, strong, and self-reprogrammable mechanical metamaterials."
To address the Von Neumann probe's challenge, NASA used prefabricated "voxels" or standardized reconfigurable building blocks. A voxel structural unit is a mechanical metamaterial building block mass-produced from high-performance fiber-reinforced composites. They offer diverse material properties by recombining constituent materials and geometry.
The self-assembling robotic system comprises three mobile robots, a path-planning algorithm, and 12-inch (30 centimeters) mechanical metamaterial units reinforced with fibers. The transport robots position the lattice units externally, while the fastening robot internally secures each newly placed block to the structure.
The two mobile robots that navigate the outer surface and interior of the system are responsible for tasks like placing objects, transporting items, and fastening components securely. By leveraging the inherent lattice periodicity of the system, they ensure precise and reliable execution of their functions. Meanwhile, simple robots use passive alignment features to achieve precise movement within the structure without needing external sensing or control systems.
The robot also features a closely integrated design, which ensures robust assembly and reconfiguration, forming a joint robotic structural system. The researchers believe this innovative strategy can shift the complexity of autonomous assembly from hardware to software since it relies on sophisticated scheduling and planning algorithms rather than intricate perception requirements.
When the scientists tested its efficiency, the system efficiently arranged 256 units for constructing a shelter with substantial strength, ultra-light density, and stiffness. The structure was built within a continuous runtime of 4.2 days. It was reported that each robot showed autonomous capabilities by executing numerous operations and encompassing tasks like voxel placement, locomotion, and fastener bolting.
RELATED ARTICLE : 'Harry Potter' Invisibility Cloak Now Real? Metamaterials Development Will Allow You to Blend With Your Surroundings
Check out more news and information on Metamaterial in Science Times.