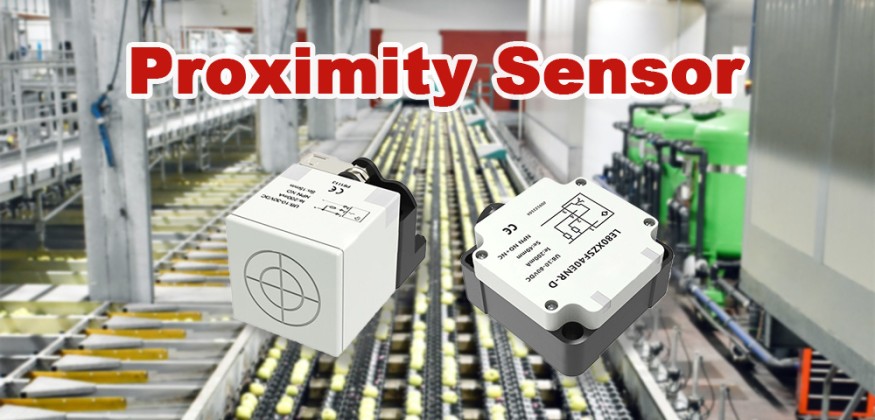
Inductive proximity sensors play a fundamental role in industrial automation, providing reliable detection and measurement capabilities in various applications. In this comprehensive guide, we will delve into the world of inductive proximity sensors, examining their functionality, applications, and the latest advances driving innovation in the field.
How does the inductive proximity sensor work?
At the heart of many industrial automation systems are inductive proximity sensors. These sensors operate on the principle of electromagnetic induction, detecting the presence or absence of metallic objects without physical contact. By emitting an electromagnetic field and measuring changes in impedance, inductive sensors can accurately detect objects within their detection range.
Types of Inductive Proximity Sensors
Inductive proximity sensors come in different types, including cylindrical, rectangular, and ring sensors, each tailored to specific applications and environments. Cylindrical sensors are commonly used for general-purpose detection, while rectangular sensors are ideal for applications requiring precise object positioning. The ring sensors offer unique capabilities for detecting objects with different shapes and sizes, making them suitable for specialized applications.

Applications of Inductive Proximity Sensors
Inductive proximity sensors are widely used in various industries, including manufacturing, automotive, packaging, and robotics. In manufacturing, these sensors are employed for object detection, presence sensing, and position feedback in conveyor systems, assembly lines, and material handling equipment. In the automotive industry, inductive sensors are used to detect parts during assembly processes and ensure precise positioning of components.
Dilemma and Development of Inductive Sensors
Recent advancements in inductive proximity sensor technology have focused on improving performance, reliability, and versatility. Manufacturers are introducing sensors with enhanced detection ranges, higher switching frequencies, and increased resistance to environmental factors such as temperature fluctuations and electromagnetic interference. Additionally, advancements in miniaturization and integration have led to the development of compact sensors suitable for applications with space constraints.
Integration with Industry 4.0
The integration of inductive proximity sensors with Industry 4.0 principles has revolutionized industrial automation. These sensors can now communicate wirelessly or through industrial networks such as Ethernet/IP and Profibus, enabling real-time monitoring, data collection, and predictive maintenance. By incorporating inductive sensors into smart manufacturing systems, companies can achieve higher levels of efficiency, productivity, and flexibility.
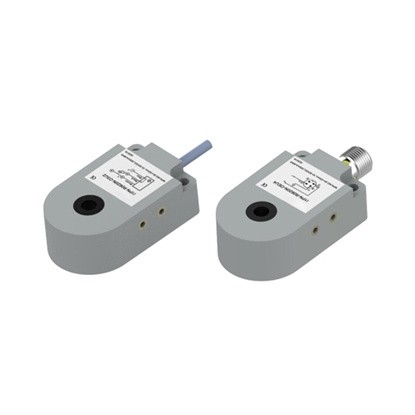
Challenges and Solutions
Despite their numerous advantages, inductive proximity sensors may face challenges such as false triggers, interference from nearby objects, and limited detection distances. Manufacturers are addressing these challenges through the development of advanced signal processing algorithms, shielding techniques, and adjustable sensitivity configurations. Additionally, ongoing research aims to improve the reliability and performance of sensors in complex industrial environments.
Integration with Hostile Environments
Inductive proximity sensors are increasingly used in hostile environments where traditional sensors may struggle to operate effectively. These sensors are designed to withstand extreme temperatures, vibrations, and contaminants, making them ideal for applications in industries such as mining, oil and gas, and heavy machinery. With robust housings and protective coatings, inductive sensors ensure reliable performance even in the harshest conditions, contributing to enhanced safety and productivity in demanding industrial environments.
Advances in Detection Technology
Recent advances in detection technology have led to the development of specialized inductive proximity sensors with enhanced capabilities. For example, sensors equipped with temperature compensation mechanisms can maintain precise detection performance over a wide range of temperatures, ensuring consistent operation in fluctuating environmental conditions. Additionally, sensors with adjustable sensitivity settings and configurable output options provide greater flexibility and customization to meet the specific requirements of various applications.
Impact on Efficiency and Cost Savings
The integration of inductive proximity sensors into industrial automation systems has proven to be a game-changer in terms of efficiency and cost savings. By accurately detecting the presence or absence of objects in real-time, these sensors enable precise control of machinery and equipment, minimizing downtime and reducing the risk of costly errors or accidents. Furthermore, the predictive maintenance capabilities of inductive sensors help identify potential equipment failures before they occur, allowing for proactive maintenance interventions and further reducing operational costs.
Future Perspectives and Innovation
Looking ahead, the future of inductive proximity sensors is filled with exciting possibilities for innovation and advancement. Emerging technologies, such as 3D sensing and artificial intelligence, hold promise for enhancing the capabilities of inductive sensors, enabling more sophisticated object detection and analysis. Additionally, the integration of inductive sensors with other types of sensors, such as ultrasonic and vision sensors, opens up new opportunities for multimodal detection and comprehensive monitoring solutions. As industries continue to evolve, inductive proximity sensors will continue to play a vital role in driving efficiency, productivity, and safety in industrial automation processes.
Conclusion
Inductive proximity sensors play a crucial role in modern industrial automation, offering reliable and cost-effective solutions for object detection and positioning. As technology continues to evolve, these sensors will remain at the forefront of innovation, driving efficiency and productivity across various industries. By understanding the capabilities and applications of inductive proximity sensors, businesses can harness their benefits to optimize processes and remain competitive in today's dynamic market.