Car manufacturing firms like Ford shifted their production focus fast during the onset of the pandemic, from automobiles to face masks and ventilators.
To make this shift possible, these companies depended on people who worked on an assembly line, a Tech Xplore report specified.
Assembly-line robots are great, but usually at only one thing. A new tool from #UWAllen & @ME_at_UW would enable manufacturers to rapidly get a grip on changing production needs by 3D printing passive grippers customized for various objects. #SIGGRAPH2022 https://t.co/PgUzfLsAUT pic.twitter.com/nOxMatBVp2
— Allen School (@uwcse) July 28, 2022
It would have been quite a challenge for robots to make such a transition since robots are tied to their regular tasks.
Theoretically, a robot invention could pick up almost any object if its grippers could be swapped out for every task. To keep the costs inexpensive, such grippers could be passive, which means that they pick up objects sans changing form or shape, akin to how tongs on a forklift are working.
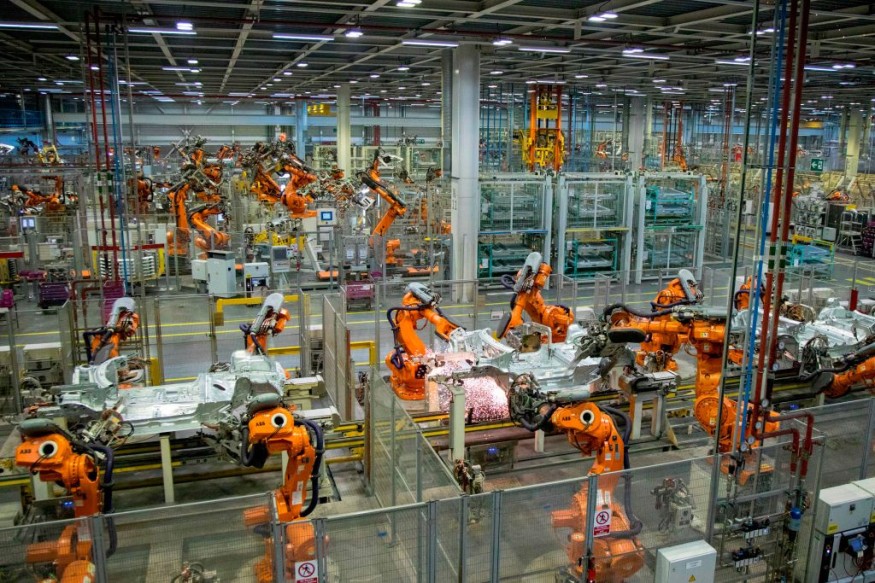
The Ability to Pick Up Any Object
A team from the University of Washington has developed a new mechanism that can design a 3D-printable passive gripper and compute the best path to pick up an object.
The team tested the system on a suite of more than 20 objects, including a 3D-printed bunny, a tennis ball, a doorstop-shaped wedge, and a drill. Both the designed paths and grippers were successful for 20 of a total of 22 objects.
The university website reported that two of the objects successfully picked up were "the wedge and a pyramid shape with a curved keyhole," the university website reported. The team is set to present its findings at SIGGRAPH 2022 on August 11.
According to the study's senior author Adrian Schulz, an assistant professor in the Paul G. Allen School of Computer Science, they are still producing most of their items with assembly lines, which are great but extremely rigid.
He added that the pandemic showed them that there is a need for them to have a way to repurpose these product lines easily.
Passive Grippers
The main idea is to develop custom tooling for these manufacturing lines, continued explaining to the senior author of the study published in ACM Transactions on Graphics.
He added that a simple robot could perform a single task with a specific gripper. Then, when the task is changed, the gripper is also changed.
Essentially, passive grippers cannot adjust to fit the object being picked up. Therefore, traditionally, objects have been designed to match a specific gripper.
UW assistant mechanical engineering professor and co-author of the study, Jeffrey Lipton, said the " tongs on a forklift "are the most successful passive gripper worldwide is the "tongs on a forklift."
However, the tradeoff is that forklift tongs only work well with particular shapes like pallets, which means that anything one would want to grip needs to be on a pallet.
In this object, the co-author explained they don't intend to pre-define the geometry of the passive gripper. Rather they want to "take the geometry of any object and design a gripper."
Limitation of the Mechanism
One limitation of this approach is that passive grippers cannot be designed to pick up all objects. Whereas it is easier to pick up things that differ in width and have protruding edges, objects with evenly smooth surfaces like a water bottle or a box are difficult to grasp, minus any moving parts.
Still, the study investigators were encouraged to see the algorithm do so well, especially with some more challenging shapes like a column with a keyhole at the top.
The path this algorithm came up with for that one is a fast acceleration down to where it's getting close to the object.
As a master's student at the Allen School and co-author of this new research, Yu Lou completed this research.
Related information about assembly-line robots is shown on BMW Car Factory Robots' YouTube video below:
RELATED ARTICLE : Multi-Fingered Robot Hand Developed to Perform Multiple Human Tasks
Check out more news and information on Robots in Science Times.