Robotic engineers showed in a new study that it is possible to make programmable analog circuits that control the actions of soft robots by processing information encoded in bursts of compressed air.
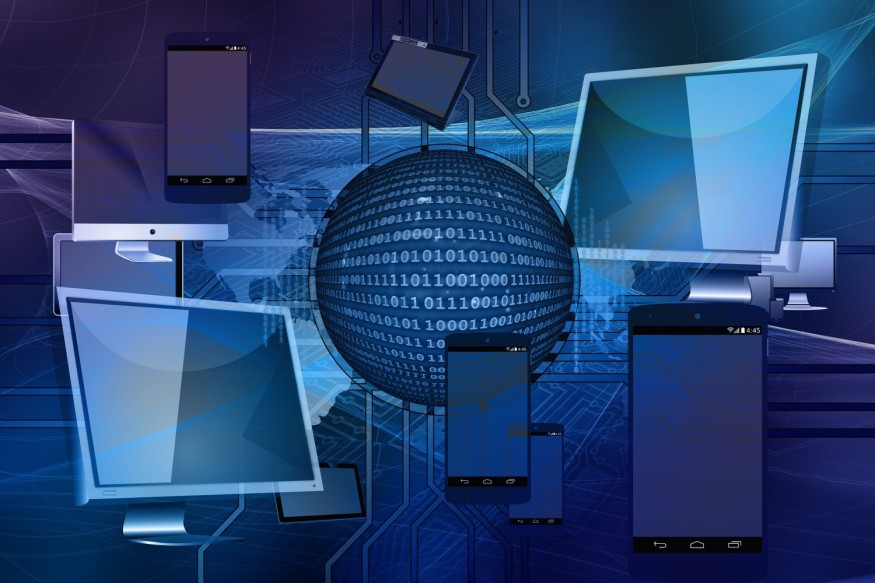
Combination of Analog and Digital Function on Soft Robots
Daniel Preston, an assistant professor of mechanical engineering at Rice, said that the biggest achievement in the study, published in Proceedings of the National Academy of Sciences, is the incorporation of both digital and analog control in the same system architecture. He claims that having both means that the pneumatic control circuits can be programmed digitally, using the ones and zeroes of a traditional computer. They can, however, bring in analog capabilities as well as continuous capabilities. He added that it enables them to significantly simplify the overall system architecture and achieve new capabilities that were not previously available.
Lead author Colter Decker and his colleagues developed two components, such as a piston-like actuator and a valve. The actuator converts air pressure into mechanical force, while the valve has on and off states that can be toggled.
Plastic drinking straws, flexible plastic tubing, rubber bands, parchment paper, and thermoplastic polyurethane sheets were used to make the components, which could be bonded together with a desktop heat press or a hot iron.
The researchers demonstrated that the two components could be combined into a single device, a bistable valve that functions as a switch and uses air pressure as both input and output. A specific amount of air pressure is required to flip the switch from off to on. Rubber bands hold the valves closed, and they are programmed by adding or removing rubber bands, which changes the amount of pressure required for activation.
Decker demonstrated that the circuits could be used to control a soft, hand-shaped robot, a pneumatic cushion, and a shoebox-sized robot that could walk a predetermined number of steps, retrieve an object, and return to its starting point.
The Strength and Goal of the Soft Robot Study
Decker stated that one of the system's strengths is its ability to reduce computation to its fundamental components. Electronic control systems, he claims, have been honed and refined for decades. Creating computer circuitry with analogs to pressure and flow rate instead of voltage and current made pneumatic computation easier to incorporate.
He also stated that the goal was never to completely replace electronic devices. In many cases, soft robots or wearables only require a few simple movements to be programmed. The technology demonstrated in the study could be much cheaper, safer, and more durable than traditional electronic controls.
ALSO READ: Scientists Created a Method To Assist Soft Robots in Moving Through Tight Spaces
Exceptional Authors
According to Science Daily, Decker began working in the lab of Daniel Preston, an assistant professor of mechanical engineering at Rice, as a freshman. Decker became interested in fluidic control systems after winning a competitive summer research fellowship that would allow him to spend a few months working in the lab of Harvard chemist and materials scientist George Whitesides.
Decker collaborated on the study with nine other authors, including co-corresponding authors Preston and Whitesides. The project became a months-long collaboration between the two research teams.
Preston stated that Rice's undergraduates are truly exceptional. In his case, Colter has risen to essentially the level of a Ph.D., student in terms of some of his output as an undergraduate researcher.
Check out more news and information on Technology in Science Times.